Designing and Packaging for Sterile Medical Products: Contact Lenses
By: Priorclave North America
Categories: Lab Autoclaves Lab Innovation

Globally, contact lenses are a $9.6 billion (USD) industry that’s expected to grow to $15.2 billion over the next decade. Much of that has been made possible by silicone hydrogel contact lenses. Developed in the late-1990s/early-2000s, silicone hydrogel lenses have been transformative, making affordable daily-wear contacts a reality. This is because, in contrast to earlier lens materials, silicone hydrogel lenses are extremely permeable to oxygen, allowing the eye to “breath” as it naturally would, even with a lens in place. Such lenses are thus not just good for consistent daily wear, but also allow for extended wear (i.e., disposable contact lenses that can be worn overnight for several days) and even “continuous wear” (wearing the same disposable lenses continuously for up to a month).
But there’s a catch: the same qualities that have made silicone hydrogel lenses comfortable for extended wear also made them potential pathogen vectors. For example, some studies have found that bacteria (including those most often associated with inflammation of the cornea) adhere to new, unworn silicone hydrogel lenses more readily than they do to other soft contacts—and up to 20 times better than other bacteria.
Clearly, delivering sterile contact lenses is a must. But maintaining an absolutely sterile “clean room” production line for disposable contact lenses is also clearly out of the question—it would drive up costs enormously, defeating the purpose of single-use lenses and denying corrected vision to billions of people globally.
Sterilizing contact lenses after sealing them in their packaging, so that there is no opportunity for viable bacteria to gain a foothold, solves this problem—hence, the importance of the blister pack in getting contact lenses to customers around the world.
Maintaining Sterility with Blister Packs
Although extremely annoying when used to package batteries and other common purchases, blister packs have been an extremely important innovation for delivering medical treatments.
Sealed and lightweight they don’t just protect contents from pathogenic contamination. The factory-sealed blister pack also enhances the integrity of the product itself, improving shelf life while providing a barrier against tampering. Even more importantly, that pristine blister pack imparts confidence to the end user.
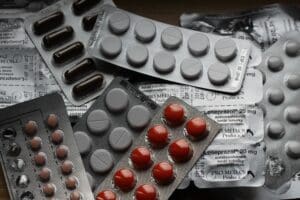
credit: Shubjt
But blister packaging is also inherently challenging in terms of maintaining sterility during production. Unrolling the thick plastic of the “forming film” (that’s the harder plastic “blister” portion of the blister pack) generates static electricity that can draw in contaminants that then adhere to the surface of the warm, freshly formed plastic. The same can happen with the thinner “lidding” material, which then may draw in further contaminants. While that may not be a big deal with cold pills (where your digestive system will easily destroy any pathogens drawn in this way), it’s much more concerning with silicone hydrogel contact lenses.
The obvious solution is essentially no different from the age-old process of canning preserves or soup: fill and seal the containers prior to sterilization. But that’s easier said than done. Blister packs are made from flexible thermoplastic—-not tin and steel. The pressures and temperatures vital to sterilizing a packaged item would warp, if not burst them.
“This sort of thing is very sensitive,” according to Tony Collins, Managing Director at Priorclave Ltd. “Not simply because the packaging itself can be damaged by the process, but because no one is going to want to buy or use contact lenses if the packaging is bent all over.”
Air-Ballasted Priorclaves for Precise Pressure Control
Priorclave has been outfitting contact lens manufactures with both R&D and production autoclaves for more than 20 years. At the beginning of the era of silicone hydrogel lenses, they were helping prominent manufacturers develop their production process.
“We’ve done it in quite a few places over the years,” Tony Collins says “The issue is that you have contacts in blister packs. In order to sterilize the lenses, they need to go in the blister pack, which is sealed, and then the entire package is sterilized. But you need to precisely control the pressure so that the blister pack doesn’t stretch, bend, or rupture. Our control system, as standard, can control the pressure coming up and going down, which is vital to accomplishing that.”
Today Priorclave offers many air-ballasted models, both for research and development of new packaging, and for use on the production line by established optical suppliers.